Environmental
Commitment
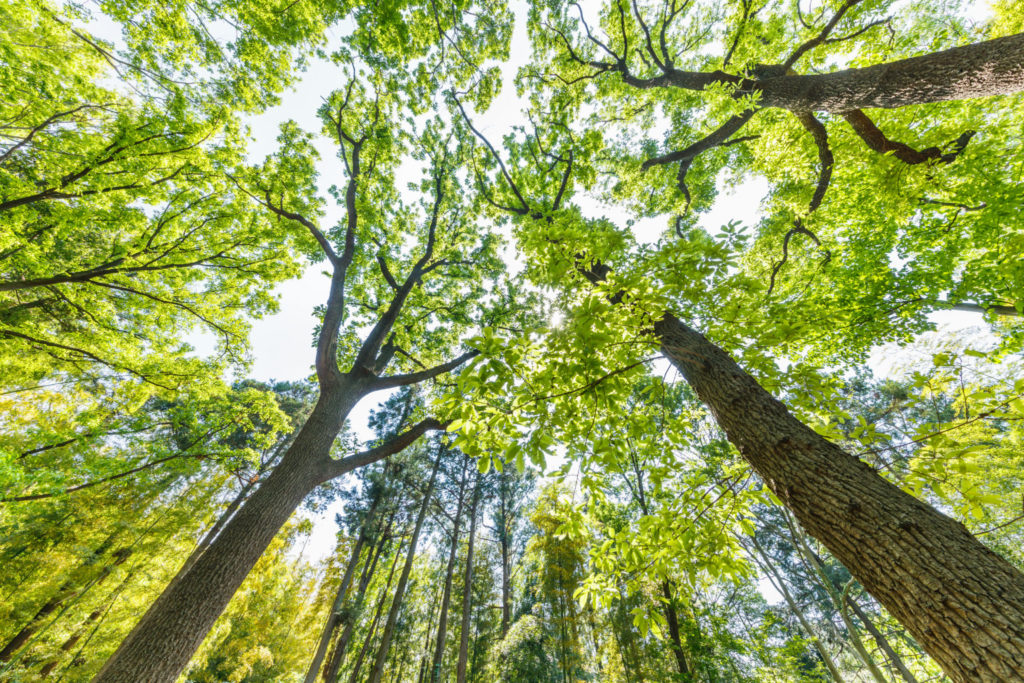
MATHESON’s policies and systems actively promote conservation of energy and resource materials, as well as investments in control, abatement, and compliance initiatives to protect our air, water, and land.
Our Environmental Management System (EMS) establishes procedures and controls for compliance:
- direct energy
- consumption and conservation
- carbon footprint
- materials usage
- waste management/recycling
- air emissions (NOx, SOx, ozone depleters)
- water use/recycling
- chemical spills and releases
- goal setting
- disclosure
- employee/management training
- audits
- management review
- pro-active measures for energy-efficiency at our Air Separation Units (ASUs), liquid CO2 plants and HyCO hydrogen generation plants
- fuel conserving strategies for our vehicles and distribution logistics
Environmental Projects
Implementing Renewable Solar Energy to Reduce Carbon Impact
MATHESON, Eloy and Coolidge, Arizona
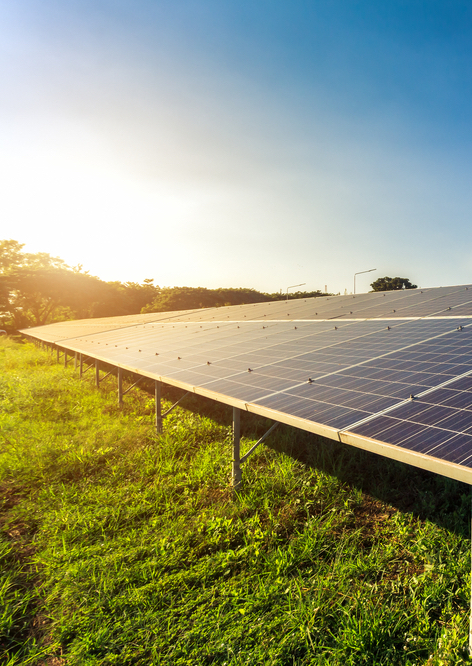
MATHESON is now receiving renewable energy from the newly operational 100-megawatt (MW) Central Line Solar plant located in Eloy and Coolidge, AZ.
Central Line Solar is owned and operated by The AES Corporation (NYSE: AES) and is the second project developed by AES to serve SRP’s Sustainable Energy Offering. SRP is a community-based, not-for-profit public power utility and the largest electricity provider in the greater Phoenix metropolitan area.
According to Bill Tolen, Director of Bulk Production at MATHESON, “MATHESON is pleased to participate in the SRP Sustainable Energy Offering. It has provided MATHESON with the opportunity to map out a future of stable energy costs while also reducing our indirect carbon emissions dramatically. The SEO program is a smart initiative that benefits SRP, SRP’s customers, and the community at large.” Tolen continued, “It is truly a win-win-win situation.” Hermann Miskelly, Senior Vice President of Quality for MATHESON, also stated, “We are proud to participate in the SRP Energy Offering, both leveraging and expanding our ongoing sustainability effort to reduce MATHESON’s CO2 footprint.”
Installing Recovery Skid Reduces CO2 Emissions
CCPI, Martinez, California
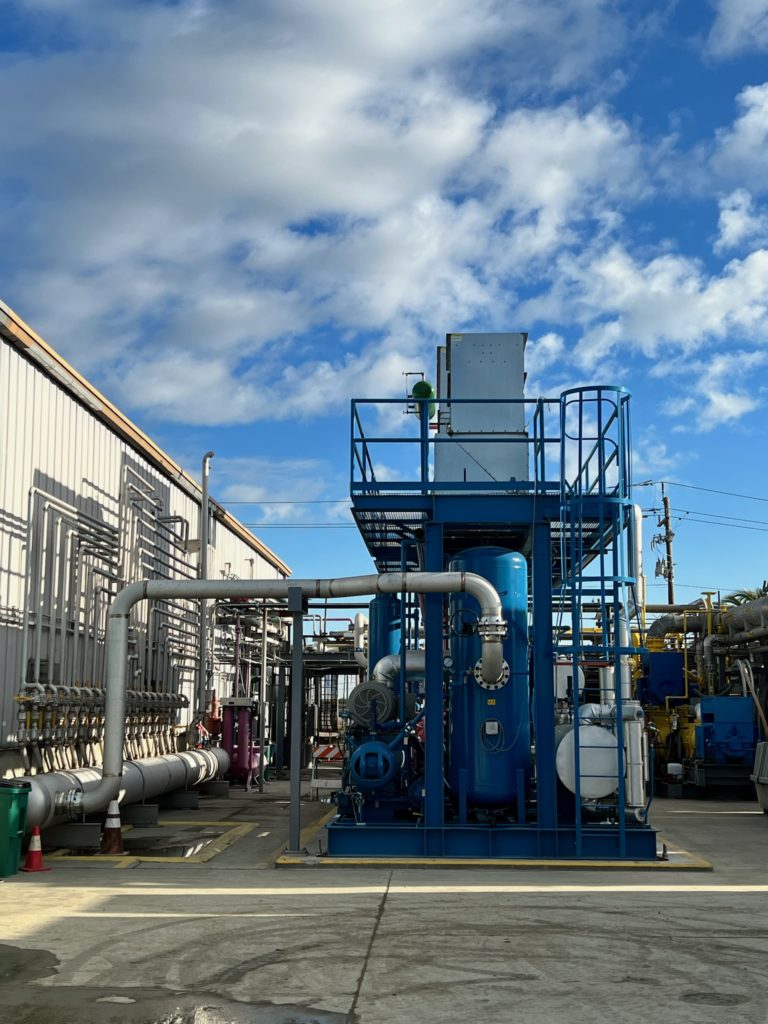
Ice production at Martinez, California was not being recovered. This led to a significantly higher ratio of liquid to solid ice production. The solution was to install a recovery skid to reduce the ratio of liquid CO2 required for solid ice production.
The skid was refurbished from original condition which avoided the capital cost of completely new equipment. During refurbishment, the skid was also converted from using ammonia as a refrigerant to R449 which allowed the Martinez plant to be removed from the CALARP (California Accidental Release Prevention) program. The skid is capable of 50 TPD of recovered product with a reduction of 46% of CO2 vented to atmosphere during recovery. CO2 is the primary greenhouse gas emitted by human activity. Estimated annual savings by recovering product is approximately $1 million.
Reducing Heater Run Time Saves Energy
MATHESON, San Antonio, Texas
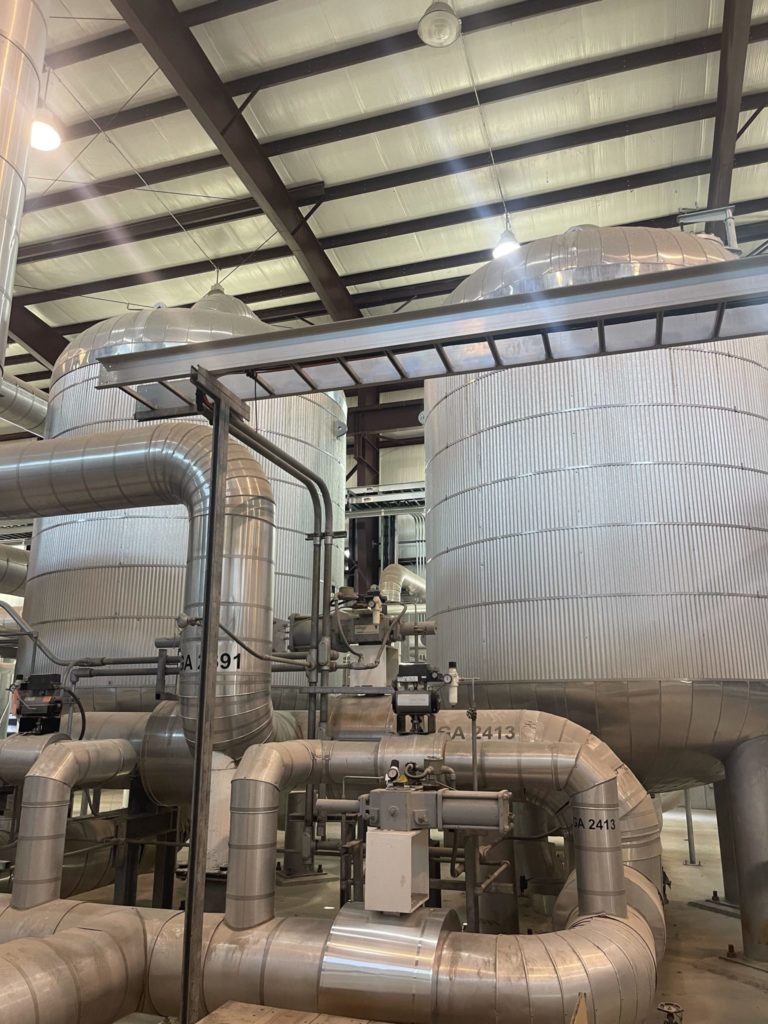
With the final products of an Air Separation Unit (ASU) reaching temperatures of -325 °F, front end purification is essential to the efficient operation of the process.
The most common way to purify the air at the front end of an ASU is to use vessels that contain an initial layer of aluminum silica to remove the majority of moisture, then molecular sieve material that will remove any remaining water vapor as well as other impurities that could freeze and plug the process, such as; carbon dioxide, nitrous oxide, and hydrocarbons.
The molecular sieve works by adsorption and can only contain a certain amount of impurities. Once the material is saturated, it must be regenerated to remove the impurities. This regeneration process often includes low pressures and temperatures above 200 °F. To reach these temperatures, an electric heater is often used to heat the gas stream and raise the bed temperature to a level that will release the impurities from the material.
At this particular location, the heater was staying on for an extended time and was getting the bed well above 300 °F. Although this will not damage the material, it was using more energy than necessary to accomplish the regeneration. The heater “on” time was reduced by 3.67 hours per day, which resulted in a reduction of over 1100 kilowatt hours of electricity each day.
1100 kilowatts is equivalent to 1,719 pounds of CO2 emissions daily, or 87.7 gallons of gasoline consumed daily. This is an annual reduction in Greenhouse gas of 627,435 pounds.
(data taken from USEPA Greenhouse Gas Equivalencies Calculator)
Reduction of Water in Blowdown Line
Lima, Ohio
Leaks in the blowdown line negatively affected plant efficiency by reducing heat recovery. Water in the
blowdown line has a higher energy content than fresh make up water, hence the energy difference lowers the amount of steam produced during the energy recovery step. Blowdown line manual and control valves were replaced to increase steam production for the given amount of natural gas consumed.
Reduction in Water Usage
Hahnville, Louisiana
Water usage was higher than necessary due to efficiency of the trailer spray procedure. A modification was made to reposition the spray nozzles at the front and rear of the trailers to allow the cooling water to maintain 100% coverage of the cylinders while increasing the amount of water returning to the sump.
Onsite Transportation – Going Greener
New Johnsonville, Tennessee

Using electric golf carts (instead of fossil fuel powered vehicles) for onsite transportation was the starting point. Then, the MATHESON team In New Johnsonville, Tennessee recently started installing solar panels on the golf carts used to get around the facility. So now, instead of grid power to charge the batteries, these carts are using renewable solar power.
Battery-powered vehicles may be zero-emission vehicles, but the source of the electricity used to charge the batteries must be considered:
Grid electricity is typically produced by the combustion of fossil fuels, and with that comes the production of greenhouse gases and other pollutants such as sulfur oxides, nitrogen oxides, and particulates. The switch to solar power is a switch to clean, renewable “green” power, and it comes with the added benefit of lowering the utility bills.
Recent Environmental Awards
2022
- MATHESON recognized as Outstanding Participant at SRP (Salt River Project) 2022 Champions of Sustainability event in Scottsdale, Arizona
- Compressed Gas Association Environmental Recognition Award for Leak Detection and Reduction at Packaged Gas Plants
2019
- Compressed Gas Association Environmental Recognition Award for Contaminated Toxic Gas Reclamation Process
2018
- Compressed Gas Association Environmental Recognition Award for Liquid Recovery and Re-Insulation – Fort Meade, Florida
- Compressed Gas Association Environmental Recognition Award for Chlorine Blow-off Reclamation –
New Johnsonville, Tennessee
Supporting Information
The Case for Blue Hydrogen
Hydrogen is essential in petroleum refining, enabling the production of clean-burning fuels, the processing of vegetable fats for green fuels, and other applications supporting the environment. But the production of hydrogen itself involves feedstocks and processes that give us a range of viably sustainable product, from “black hydrogen” (produced from coal) to green hydrogen (produced from 100% renewable resources). This article describes the many colors of this colorless element, and the work toward cleaner, more environmentally resposible hydrogen supply. >>Read More
Hydrogen in the Production of Drop-in Green Fuels
If green fuels are the goal, then blended source fuels represent the practical pathway to green. Renewable fats (animal- and plant-based) can be converted to renewable diesel, jet fuel, and naphtha. A key step in the process is the hydrogenation of the organic fats at elevated temperature in a catalytic reactor. The end products are fuels that at the molecular level are nearly identical to their petroleum processed counterparts. This article describes MATHESON’s technology to provide the necessary hydrogen to “green-up” the fuel end-product. >>Read More
Getting the Most from Your Hydrogen Plant, Part 1
This webinar discusses several topics associated with the optimal operation of a hydrogen production process. MATHESON engineers are targeting integration of H2 production in the production of green fuels (including drop-in green fuels); optimized reformer operation; and renewable hydroprocessing projects. The webinar deals with these topics in the context of end-to-end hydrogen production operations. >>Read More
Remote Management of Hydrogen Production
While the technologies and operational efficiencies of remote plant management may not seem directly related to “Environmental Commitment,” hydrogen production itself provides critical leverage toward lower allowable sulfur content in gasoline, diesel, marine fuel oil (IMO 2020), and maintenance of high cetane in diesel. To the extent that steam methane reforming (as well as other H2-production processes) is energy intensive, it only makes sense that it is important to maximize the efficiency of the process and minimize emissions from a sustainability perspective. This article provides a detailed overview of the critical advantages of remote operations management. >>Read More